British Sugar: Managing Health, Safety, Security and People With Access Control

14 January 2021
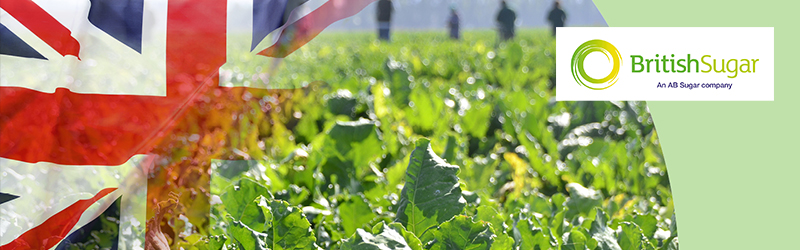
British Sugar is the sole processor of
the UK’s beet sugar crop, they work in partnership with around 3,000 growers
and their customers to deliver a world-class product that is made to the
highest standards.
Operating across four advanced
manufacturing plants, British Sugar have become the leading producer of sugar
for the British and Irish food and beverage markets. Access
control has played a key role in effectively managing the health and safety, security
and people within each of these sites.
Requirement
The main
use of access control at British Sugar is to manage entry around the perimeter
of their manufacturing plants. Additional controls are used to restrict access to
potentially hazardous areas and additionally provide auditable traceability
around sensitive food processing areas.
British Sugar rely heavily on their systems to enable their
manufacturing operations to operate both efficiently and safely. With their
current legacy system now unsupportable, British Sugar were struggling to
implement any system changes or updates. As a group, the decision was made to upgrade their access control system
across all four of their manufacturing sites.
The decision to upgrade with TouchStar ATC was based on an
existing relationship which had spanned over a decade. Clive Gray, Technical Transformation Analyst at British
Sugar comments, “We were operating on TouchStar’s MicroTrak IP+ system which
was over 10 years old. As a solution, it had more than proved itself, however
it was now a legacy system that was essentially unsupported, so we knew we had
to upgrade. We know TouchStar install quality systems, so it made sense to
start talking to them about how we could move on to a future proof system that
would allow us full support on the latest windows operating platform”.
Implementation
With all four manufacturing sites producing up to 1.4
million tonnes of sugar, 365 days a year, both TouchStar and British Sugar were
looking to ensure a smooth rollout of the proposed system upgrade. As the
long-term incumbent supplier to British Sugar, TouchStar had experience of not
only the legacy system, but also each of the manufacturing sites to be upgraded.
Lynden Jones, Managing Director of TouchStar ATC continues, “We were delighted
to have had the opportunity to work alongside British Sugar on the upgrade
project. We worked closely with both Clive and the British Sugar IT Team,
specifying the system requirements, confirming both the site layouts, and
wiring structure so we could plan for a staged upgrade with minimal
disruption”.
Solution
The new system was successfully installed across the sites
in Bury St. Edmunds, Cantley, Newark and Wissington . As part of the upgrade,
new proximity card readers were installed, replacing the existing magnetic
swipe technology. During the phased rollout, TouchStar provided a card upgrade
plan that enabled British Sugar to utilise one card that uniquely worked on
both the legacy system and new system, thus allowing for a more efficient rollout
of the new processes.
TouchStar’s own Evolution Software, a modular based access
control system provided the upgraded interface. TouchStar designed the new
system to fit around the existing cabling structure thus avoiding the additional
project costs associated with a full site rewire. Utilising a backward
compatible controller solution, British Sugar were also able to utilise the existing
cabling type to provide a much wider point to point networked area than that of
a traditional networked solution.
Results
and Benefits
Since the installation, British Sugar are now looking to migrate
their Head Office from the off the shelf type system onto the new TouchStar
solution. Additional entrances, such as their delivery points are being
reviewed with respect to potential reader upgrades and enhancements including integration
of emergency roll calls into their security and mustering system are also being
considered.
Clive continues, “What was important to us was ensuring a
smooth rollout, particularly as the upgrade did partially coincide with our
busiest time of year. TouchStar worked closely with us throughout the whole
upgrade process, helping ensure a successful rollout with minimum disruption. Not
only that, they have upgraded us to a great system, which is what we have come
to know them for. We are thrilled with the potential the system now offers us
for additional enhancements and look forward to working TouchStar on future upgrade
projects”.